5 Spring Claims To Avoid
Our GEICO | BoatUS Marine Insurance claim files highlight the most common springtime problems. Here’s how to avoid being one of our statistics.
- January 17, 2024
Last spring, a GEICO | BoatUS insured was readying his 27-foot cruiser for launch. He checked the bilge pump, fuel lines, and stuffing box and did his usual thorough inspection from bow to stern. He thought about replacing the engine’s raw water impeller but figured he could get one more year out of it. Big mistake. On his first trip out, after he got onto plane, the engine overheated and shut down suddenly. After he was towed back to his marina, his mechanic said that the overheat had destroyed his engine. The cost to repair? Nearly $14,000. Unfortunately, damage caused by a worn-out impeller is considered maintenance and usually not covered by a boat’s insurance policy.
Don’t let something like this ruin your season (and wallet). BoatU.S has been insuring boats for decades, and our detailed claims analyses let us spotlight where things go wrong. What follows are the most common claims we see every spring, some from winterizing mistakes and some from a neglected spring commissioning routine.
Flooding or Sinking
Aged underwater hoses and fittings are the single most common cause of sinkings, according to several analyses we’ve done over many years. The biggest culprits? Corroded fittings, old hoses, rusty hose clamps, leaking stuffing boxes, and split bellows.
Before you launch, make sure hoses fit snugly and are double-clamped where possible. Those showing signs of age — rot, stiffness, bulges, leaks, and/or cracking — should be replaced. Clamps tend to corrode on the bottom where it may be hard to see. Inspect thru-hulls for corrosion or cracking, and make sure seacocks operate easily so you can close them in an emergency.
And after you’ve checked all your underwater fittings before launching, check them again after the boat is in the water, just in case.
In one claim, the owner said that water in his cockpit always drained well. Then a series of unfortunate events resulted in a (preventable) at-the-dock sinking. Rain during a heavy spring downpour dumped gallons of water into the cockpit, which, due to a badly deteriorated hose, drained into the bilge rather than overboard. The vessel had no operational bilge pump, and the excess amount of bilge water caused the boat to settle, submerging the thru-hull and sinking the boat.
Stuffing boxes have always figured high on the list for dockside sinkings based on our claims analyses. Stuffing boxes should never leak at rest and only leak a drop or two per minute while underway. If leaking can’t be stopped by tightening the nut, repack the gland. Be careful, though: Overtightening the nut may prevent leaking underway, but can burn out the packing material. If you’re ready to upgrade to a dripless seal, read “How To Install A Dripless Shaft Seal” for step-by-step instructions and a video on how to do it.
Intake strainers that weren’t drained properly in the fall could’ve been cracked or split by ice over the winter. There have also been claims for strainers that weren’t closed completely after winterizing as well as hoses that weren’t resecured. Other claims have been for corroded strainers that fell apart while underway.
Bilge pumps are not there to prevent boats from sinking in serious flooding. Their job is to remove nuisance water and, at best, buy you a little time to fix what’s leaking. But for them to do that, you need to make sure your bilge pump is working. The best way to make sure the pump and switch are working is to do what Mother Nature would do: add some water to your bilge. You’ll instantly know if all parts of your system are working. If not, check electrical connections at the pump and switch, which are the most common areas for failure. Also make sure they’re not made using wire nuts as shown in the photo below (a definite no-no!). See “Bilge Pump Basics” to learn more.
Sterndrive bellows have to remain watertight for years while withstanding flexing and bending, exposure to water and marine growth, and extremes of temperature. And there is usually more than one. The shift bellows is the smallest, which makes it most susceptible to cracks that start in the folds. By tilting and turning the sterndrive you can inspect the bellows. Marine growth can puncture the bellows, so remove any that you find. Replace the bellows if you see any sign of wear, but at least every five years. If one bellows is worn, chances are all of them are, so replace them as a set.
Engine/Outdrive Damage
Impellers can last a few years under normal operation, but many boat owners simply replace them annually as cheap insurance. A damaged impeller can cause severe overheating if not caught quickly, potentially leading to a smoking-hot exhaust hose in the engine space, or even a fire. Even if a failed impeller doesn’t melt an exhaust hose, missing bits can become lodged in the cooling system, blocking passageways and further reducing engine-cooling ability. Once that occurs, you’ll need to disassemble the cooling system to remove these parts, another expense that can be easily avoided.
How long do manifolds last? Obviously, the way you use your boat will be a factor, as will the type of water it’s used on. Saltwater boats are going to see a shorter manifold life when compared to their freshwater counterparts. Most experts suggest that a manifold will have a life expectancy of six to eight years. A clogged manifold will cause the engine to overheat, while a leaking manifold allows water into the engine, which can destroy it. One thing is for certain: The older your manifold gets, the more likely it is to fail.
Tip: If you see rust streaks on the outside of the manifold, you can be sure there is leaking somewhere.
Leaking oil or other fluids can quickly ruin an engine or sterndrive if they’re run without them. Before you even move your outboard or sterndrive boat from its winter resting place, check underneath the lower unit and make sure there are no spots of leaking oil. If so, find out what caused it before you launch. Even if you changed the lower unit oil last fall, verify that it’s still topped up. Low coolant and poor lubrication can cause an overheat and damage an engine, and insufficient fluid can destroy a transmission. If the owner of this scorched transmission had only checked his fluid level, he wouldn’t have had to take a second job to pay for repairs.
Fire or Explosion
Fuel lines, including fill and vent hoses, have the potential to leak flammable gas and fumes and cause an explosion or fire. Carefully check them for indications of softness, brittleness, or cracking. Any that are suspect should be replaced immediately with Coast Guard-approved hose. Check joints for leaks (use your finger and look for stains under or around the fitting), and make sure all lines are well supported with non-combustible clips or straps without rough edges. Inspect all fuel-system components for leaks — fuel tanks, fuel pumps, filters, lines. A dry rag can be used at connections, or trust your nose. Clamps should be snug and free of heavy rust.
The boat’s electrical system is the cause of more than half of all boat fires, according to the claims files, and most often they are due to faults in the DC (battery) circuit. The best defense is to inspect, clean, and tighten electrical connections, especially both ends of battery cables. Loose connections can “arc,” which creates an enormous amount of heat and can cause a fire. Studs, nuts, and washers should be made from copper — not aluminum or steel. Dissimilar metals have the potential to cause galvanic corrosion on terminals. Wire brush battery terminals, and fill cells with distilled water. Many older boats have been upgraded with additional lights, fans, chartplotters, sound systems, and so on, over the years, but often the electrical wiring and panels have not, which could lead to overheated circuits.
Tip: A vapor detector can alert to a build-up of fumes in the bilge. See “CO and Fume Detectors” to learn more.
Most AC electrical fires occur in the shore power system. In addition to the cord itself, our insurance claims data pinpointed a particularly vulnerable link in the shore power chain: the shore power inlet on the boat, typically the terminals at the back of the inlet where the boat’s wiring is connected. These inlets are particularly vulnerable to water intrusion, and the connections are subject to vibration and corrosion and are often surrounded by easily ignited material. If there’s any sign of corrosion, replace them.
Loose or corroded AC connections generate heat and the potential for fire, a problem especially prevalent among vessels that continually run high-energy loads such as air-conditioning, water heaters, and the like. Plugging and unplugging shore power connectors while energized contributes to the problem. The micro-arcs and sparks generated each time you do so create tiny pits on surface connections, which in turn lead to resistance and heat buildup. Take a moment to feel your shore power cord and inlet once your boat is launched and your boat is drawing current. Warm is OK, maybe, but more than that is a fire waiting to happen.
You wouldn’t think an engine control cable would be the cause of an insurance claim, but it happens more often than you might think. In one case, a large cruiser was heading out for the first time of the season. When the skipper called for reverse in order to stop at a fuel dock, the boat kept going and smashed into a smaller boat at the dock. The cause was a nut that had come off of the transmission shift cable’s attachment point. Throttle, shift, and steering cables usually slide inside a sheath, and it’s hard to see their condition. Grab hold of one and twist it around. If you hear crunchy sounds, chances are there’s rust inside and it’s time to replace.
Trailer Breakdown
Failed tires are the No. 1 reason for our trailering claims. They’re not only a nuisance; they can cause a traffic accident. Before you hook up, inspect tire treads and sidewalls. Cracks on sidewalls or lack of tread indicates the tire must be replaced. Use a gauge to check tire pressure. Don’t forget the trailer’s spare tire. Your tire’s age (whether for a boat trailer, truck, or passenger car) can be determined by a DOT (Department of Transportation) time stamp that provides the tire’s date of manufacture.
Rust is an insidious problem that can occur inside a trailer’s axle tube as a result of trapped water. This can lead to a catastrophic failure of the axle, and it will never happen at a convenient time. In addition to the routine checks you do before each tow, each spring before launch give your trailer a more in-depth maintenance inspection for problems such as bent or twisted members, nonfunctioning lights, cracked welds, missing hardware and, of course, corrosion. To further hedge your bets while on the road, consider adding insurance coverage for your trailer through GEICO | BoatUS, which includes roadside assistance.
Failed bearings can ruin your day. A failed bearing on one insured’s trailer caused a several mile backup on the Golden Gate Bridge. Before hooking up this spring, inspect your bearings and repack or replace as necessary.
Sailboat Rigging Failures
Sailboat rigging failure, while not as common as other claims, can be catastrophic and even cause injuries. Some claims were due to turnbuckles that were loosened when the boat was hauled out, then never retightened. Also, look for corrosion, especially around the chainplates, turnbuckles, and swaged fittings. Put on a rugged pair of gloves and run your hand down the shrouds and stays. If the glove catches on broken strands, the standing rigging needs to be replaced. See “Inspecting Sailboat Rigging” for more on inspecting rigging.
You might be surprised to learn that on-the-water towing claims are actually the most common of all our marine insurance claims. “Mechanical breakdown” is the catch-all category that is the most frequent cause of these claims and includes such things as starter and belt failure, steering system problems, and lost props. A thorough inspection (use our Spring Commissioning Checklist) can prevent most of these claims.
Charles Fort
Contributing Editor, BoatUS Magazine
About Vessel Vanguard
Vessel Vanguard is a leading marine safety and maintenance management software provider dedicated to revolutionizing the maritime industry. With a commitment to innovation and excellence, Vessel Vanguard delivers cutting-edge solutions to streamline operations and enhance vessel performance and safety.
Latest Industry Insights
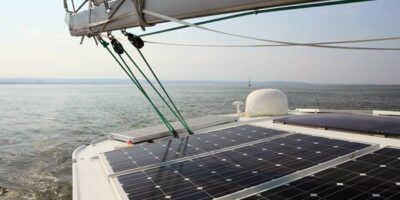
Embracing E-Boating Efficiencies
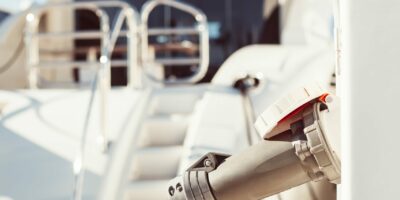
Boat Fuel Systems
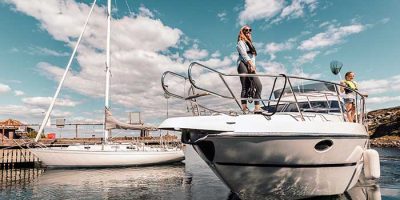
The Future of Boats & Boating
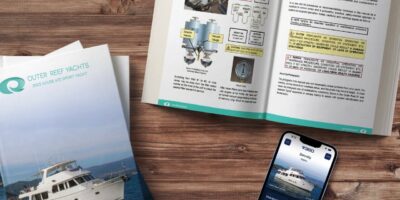
Yacht Navigation Light Inspection
View All of Our Industry Insights
Navigate maritime with the latest news, practical how-to guides, insightful analyses and more.