Maintaining Engine Temperatures
Guard your marine diesel engine against heat-related havoc. Cooling systems, heat exchangers, and maintenance prevents failures on your boat.
- January 25, 2024
Diesel engines generate high internal temperatures and this heat wreaks havoc with the various systems. In addition to keeping the engine from overheating, the cooling system on a modern diesel must also maintain the temperature of the lubrication oil, transmission oil, air intake, and fuel. This process takes place through a series of heat exchangers, as many as five on some engines. Heat ex- changers operate in a harsh environment and failures occur regularly. By under- standing how these components function and how to monitor their condition, you can greatly reduce the risk of failure on your boat.
Regardless of the application, each cooler or heat exchanger works in the same way: one liquid circulates inside a closed set of tubes while another liquid flows around the outside of those tubes. The liquid at the higher temperature exchanges heat with the cooler liquid and this process maintains critical temperatures. On a turbocharged engine, we can add another variation: using seawater to reduce the engine air intake temperature.
Engine Coolant Heat Exchanger
Marine engines rely upon two liquids to manage the internal heat generated in the combustion process: coolant internally and seawater externally. On many engines, the coolant might be proprietary from the manufacturer, with critical anticorrosion formulations. The coolant circulates in a closed internal loop, absorbing heat from the engine. Without a way to remove that heat, it’s a matter of time before heat buildup would lead to overheating. At the same time, a separate pump pulls seawater in through the sea- cock and strainer, circulating the water through hoses and pipes on the outside of the engine, and eventually exiting with the exhaust gas. These two liquids meet at the heat exchanger, allowing heat from the internal coolant to transfer to the continual flow of cool seawater.
Oil Coolers
The lubrication oil also must be kept cool. If the oil runs too hot it will be- gin to break down, losing viscosity and other critical properties. To keep the temperature down, many engines will run the lubricant through a cooler. In the most common configuration, seawater flows inside small diameter copper tubes, while the oil circulates around the tubes. Some engines circulate cool- ant through the tubes rather than sea- water to accomplish the heat transfer. Using coolant instead of seawater reduces some of the maintenance issues described below. Transmissions also generate heat and many use an oil cooler to maintain the fluid temperature.
Fuel Coolers
Modern diesel engines demand much more fuel than they burn. An engine consuming 15 gallons per hour might be running 60 gallons per hour through the fuel lines, sending the unused fuel back to the tank through the return line. This additional flow provides lubrication and cooling for the fuel system’s components. As the extra fuel passes through the system it picks up heat, returning warmer fuel to the tank. Engine manufacturers specify the maximum acceptable tem- perature for the incoming fuel. Also, warm fuel expands, re- ducing its density and therefore its efficiency.
As the fuel runs through the engine it picks up heat, send- ing warmed fuel back to the tanks. Combined with elevated engine-room temperatures, the fuel in the tank gradually heats up. To manage this heat, most modern engines run the fuel through a cooler.
Air Coolers
The seawater loop also can be directed to cool air. Turbo- chargers force more air into the engine in order to gain horse- power. Just as warmer fuel loses density, air expands with heat and becomes less dense. Less oxygen per cubic foot of air reduces combustion, causing loss of horsepower.
An intercooler uses seawater to cool the air before it is ingested by the engine. Once again, seawater passes through small tubes (in many cases combined with thin plates like car radiators), but in this case air circulates around the tubes.
Inspection And Maintenance
Heat exchangers function in a tough environment, so failures occur regularly and the situation demands vigilant maintenance.
Let’s start with corrosion. Seawater inside a metal chamber can lead to galvanic corrosion (coolers that circulate coolant do not have this issue). To prevent internal corrosion, sacrificial anodes, often referred to as “pencil zincs”, fit into the chamber of the heat exchanger, sometimes two per unit. These zincs can usually be spotted by virtue of their brass hex head caps. For most recreational boats annual replacement will be sufficient but it varies with engine hours and the water’s salinity, with most falling in the range of once every 100-200 engine hours. Find out how many pencil zincs your engine contains and have ample spares of the correct sizes aboard.
If corrosion does occur, pinholes can develop in the tubes. Once that happens, there can be an exchange of fluids. Typically the seawater or coolant circulation will be less than 15 PSI, while the oil will be at a much higher value, above 60 PSI. Since the oil pressure exceeds the water pressure, pinholes in the tubes can allow the oil to leak into the seawater. The oil then flows into the seawater loop, eventually exiting with the exhaust gasses. If you are losing oil but not finding any in the pan, you might want to remove and pressure test the oil cooler. When the engine has been shut down, it becomes possible for seawater to mix into the oil.
As seawater flows into the small tubes, debris can accumulate, obstructing the flow. As the zincs break down, small pieces release into the stream of water and over time these can accumulate downstream and restrict the flow. Failing impellers release small bits of rubber into the loop and these also accumulate at the heat exchanger, impeding flow. When an impeller has lost pieces of rubber, each piece must be located and removed downstream. When cooling efficiency starts to decline, removing the end cap from a cooler will give you access to any accumulated debris: Remember that the accumulation happens on the end receiving the incoming flow of water.
Impurities in the seawater can lead to a buildup of film and scaling on the tubes inside the cooler. Any buildup on the outside of the tubes will act as insulation, reducing the transfer of heat. To clean tubes, circulate a descaling solution through the seawater loop, or remove the heat exchanger core and send it out for an ultra-sonic treatment.
Intercoolers, on the other hand, have to cope with hot air. To further complicate the challenge, most air-cooler housings consist of cast aluminum, while the core usually contains cop- per. Air coming into the cooler contains contaminants that will cling to the cooling vanes, while seawater will gradually cause accumulation inside the tubes. This all sounds like a science experiment: let’s mix copper, aluminum, sea- water, and hot air, and see how long it lasts! For these reasons, air-cooler failures occur routinely. A failing air cooler will reduce the engine’s efficiency, re- sulting in a loss of boost pressure from the turbo. In extreme cases, the hotter air entering the cylinders can lead to premature cylinder failure or ingestion of liquid into the cylinder.
Boat owners can keep an eye on their heat exchangers in several ways. First, regular visual inspection will reveal any leaks, usually in the form of seepage. While this amount of moisture might seem benign, in time paint will slowly lift, components beneath will rust, and bilges will be stained. At the first sign of moisture or green verdigris around fittings, add this item to your to-do list.
A temperature sensing device will help you assess and monitor the internal condition (PassageMaker, Jan/Feb 2015). For the coolant/seawater heat exchanger, use a pyrometer to compare the temperature of the coolant entering to the coolant leaving. The drop should be about 10 degrees Fahrenheit. If you see a gradual reduction in the difference, chances are it’s time for some maintenance. For oil coolers, measure the delta between oil in and oil out of the cooler— in this case the drop should be in the 10-20 degree range. Transmission oil tends to stay in the 10 degree range. For fuel coolers you should also see a drop, but the main requirement here is that the fuel entering the engine must meet the manufacturer’s requirement.
Summary
Let’s start with the bad news: Modern marine diesel engines rely on a number of coolers to maintain critical operating temperatures. These coolers operate in a harsh environment and failures abound. Here’s the good news: Failures rarely happen suddenly (they only seem sudden if you haven’t been paying attention). By keeping the cooling system clean, you gain a substantial increase in horsepower and fuel efficiency. Most problems develop gradually and by monitoring temperatures, replacing zincs, and looking for visual signs of leaks, you will be able to keep your cool and maximize engine performance.
Steve Zimmerman
Zimmerman Marine
About Vessel Vanguard
Vessel Vanguard is a leading marine safety and maintenance management software provider dedicated to revolutionizing the maritime industry. With a commitment to innovation and excellence, Vessel Vanguard delivers cutting-edge solutions to streamline operations and enhance vessel performance and safety.
Latest Industry Insights
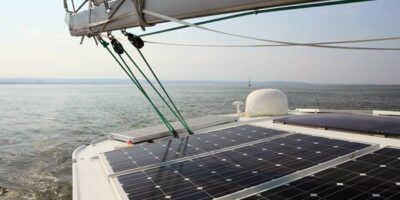
Embracing E-Boating Efficiencies
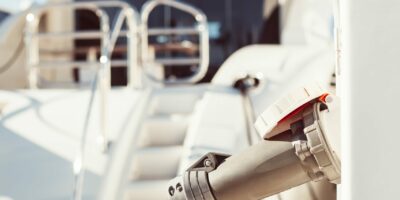
Boat Fuel Systems
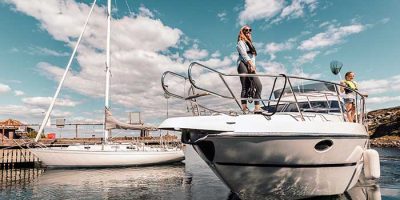
The Future of Boats & Boating
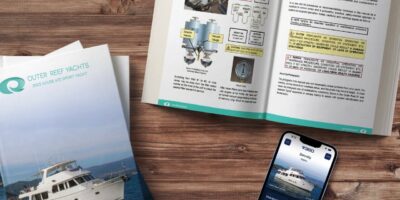
Yacht Navigation Light Inspection
View All of Our Industry Insights
Navigate maritime with the latest news, practical how-to guides, insightful analyses and more.