Battery Cabling & OCP Service
Discover crucial insights on battery cabling and high-amperage overcurrent protection, exploring ABYC standards, battery banks, fuses, and more for optimal marine electrical systems.
- January 17, 2024
There are several practical considerations that ABYC doesn’t really address about battery cabling and high-amperage overcurrent protection.
Although ABYC standards permit up to four cables to be connected to a battery stud, there are several reasons to keep the number to only one or two at most. First, because batteries are serviceable items, minimizing the number of cables reduces the chances for cables to be reconnected erroneously or omitted when replacing batteries. Secondly, the seals that prevent battery acid from escaping from around the posts are prone to weeping, which will cause corrosion of the cable terminals and corresponding resistance. Third, minimizing the number of cables that need to be disconnected and reconnected reduces the chance of an errant cable causing a short or a spark that could ignite hydrogen vapors. For these reasons, it is often a good idea to use positive and negative busses for distribution and then connect the batteries with single cables to the busses. In this article, “load” refers to anything that discharges or charges the battery.
Larger boats will have battery banks that may consist of batteries in series and/or in parallel. To maximize the life of these batteries, they need to be wired so that all batteries are charged and discharged equally. If several batteries are located side-by-side and wired in parallel, it may appear neater to connect the battery at one end to the loads, with jumpers to each subsequent battery. However, each set of jumpers will impart a voltage drop to each following set of batteries, such that the batteries further from the load will be discharged and recharged at slightly lower rates. It might seem that this would balance out, but batteries respond differently when discharging and recharging. This also results in each battery undergoing different rates of discharge/recharge cycling. To remedy this situation, the positive connection should be made to one end of the bank and the negative to the opposite end. This is called cross-taping. All intermediate jumpers should also be the same length. Boatbuilders sometimes locate batteries of one bank in different locations, but all the batteries in a bank should ideally be sited in one place, with air spaces between them for ventilation, so that all will remain as close as possible to the same temperature.
Another cabling option with paralleled batteries is to connect each battery (or series-connected batteries) individually to the positive and negative busses, again with all cabling of matching length.
It’s a good idea to have a main fuse between the battery positive terminal and the positive bus, but this may be impractical if the potential current of the system exceeds the available fuses. All loads attached to the positive bus must have overcurrent protection, with the exception of starting circuits. The short-circuit current of larger battery banks may exceed the amp interrupt capacity (AIC) of available fuses. Connecting each battery (or series-connected batteries) of a paralleled bank to the positive bus through individual fuses can provide a solution. This arrangement also allows a faulty battery to be removed from service by removing its fuse and offers the possibility of replacing the batteries without interrupting service, by individually disconnecting each fuse and replacing the corresponding battery. If separate fuses are used for each element of a bank, each must still be sized for the maximum system current, because in the event of partial system failure, any battery may be temporarily supplying the entire system.
When using 24/7 positive and negative busses, consideration must also be given to battery switches. Installing a “master” battery switch between the batteries and positive bus will provide a quick and positive manner of completely disconnecting the batteries in an emergency, but at the risk of damage to charging systems especially alternators. A master switch of this nature might best be a remotely operated switch controlled at the helm, covered against accidental use, and distinctly labeled “EMERGENCY ONLY.” Individual battery switches between the positive bus and loads should be installed, either instead of or in conjunction with an emergency master switch. Circuits to distribution panels, engines and generators, battery parallels, bow and stern thrusters, windlasses, davits, water makers, and inverters should all have disconnect switches. Loads that are permitted by ABYC to bypass disconnect switches, such as bilge pumps and alarms, smoke and CO detectors, battery chargers, alternators, solar and wind systems, and memory circuits for electronics may be disconnected, if necessary, via their overcurrent protection.
Although overcurrent protection is not required for starting circuits, it is still a good idea. In addition to total shorts in a starting circuit, starters can fail to disengage for a number of reasons such as welding of corroded starter solenoid contacts, corrosion of mechanical components, damaged spur gear or flywheel gear teeth, incorrect spur gear on a new starter. Any of these can result in the starter continuing to draw current. Battery cabling has an ampacity rating for continuous loads, based on the ability of the cable to dissipate heat caused by its natural resistance, but the cable can conduct substantially greater amounts of current. Starter current may be well in excess of the rated ampacity of the cabling, but because it is an intermittent, short-duration load, heating of the cable is a secondary concern to voltage drop. The cranking current of a starter can be measured if the engine can be prevented from firing or can be calculated from the power rating of the starter which should be available from the engine manufacturer. Note that the cranking current will be higher in colder temperatures.
Fuses have varying trip times based on the amount of overcurrent passing through them. This information should be available for each fuse type as a chart from the fuse manufacturer or retailer. For example, a given fuse may operate indefinitely at 10% overcurrent (to allow for manufacturing variations), for 2 minutes at 25% overcurrent, 30 seconds at 50% overcurrent, 10 seconds at 100% overcurrent, and 2 seconds at 200% overcurrent. If one allows for a maximum cranking window of 30 seconds (which likely exceeds any engine manufacturer’s recommendation – but may be approached when trying to achieve sufficient cylinder temperatures to start a cold diesel or to bleed a tricky fuel system), with our hypothetical fuse, and a starter that draws 300 amperes, a 200-ampere fuse would be adequate (based on 50% overcurrent for 30 seconds) to protect the starter. Ideally, this will be within the rated ampacity of the cabling.
Another consideration when dealing with high current loads and longer wire runs is that ABYC permits dual cables to be run to reduce voltage drop, as long as the maximum current and circuit protection is within the ampacity of each individual cable (in the event of one cable becoming disconnected).
Cabling for intermittent loads such a starters, thrusters, and windlasses should be sized per the manufacturer’s recommendations. For continuous-duty loads, use the manufacturer’s recommendations if they call for larger cabling than ABYC calculations recommend.
Sometimes, small-gauge negative wires are required on high-current loads or devices or are bundled with high-amperage positive cabling. Although ABYC has no requirements for these situations, consideration should be given to overcurrent protection for these wires where they connect to a negative bus or negative source, to protect these wires should they short to a high-amperage positive source. An example might be the negative control wire on a high-amperage solenoid box for a windlass or thruster. A short with a heavy gauge positive cable could turn the small gauge negative wire into a fuse.
Lithium Ion batteries and some Absorbed Glass Mat (AGM) battery banks can supply power at a much more rapid pace than wet lead acid banks. Many boats are installing systems capable of propulsion or supplying large loads like air conditioning. These battery banks can have massive storage potential and often operate at much higher voltages. Torqueedo has partnered with BMW to produce their Deep Blue battery bank that operates at 360 volts, has a capacity of 40 kWh, and weighs 612 pounds. This system can produce enough power to plane small power boats, but it should be noted that any voltage over 50 volts is lethal. Nigel Calder’s Integrel system utilizes 48-volt banks for this reason. This system uses a powerful alternator, a sophisticated controller that is aware of when the engine is being used for propulsion and ramps back on the horsepower being used for the alternator, and voltage transformers and inverters to supply power to the house loads.
Welding cable is often used in boats, as it is less expensive than boat cable, and is more flexible due to finer stranding and softer insulation. It should be avoided for two reasons. It is usually not tinned, making it more susceptible to corrosion. It also uses neoprene insulation, which will absorb oils and antifreezes and then swell to a remarkable size while becoming a gooey mess.
Steve Zimmerman
Zimmerman Marine
About Vessel Vanguard
Vessel Vanguard is a leading marine safety and maintenance management software provider dedicated to revolutionizing the maritime industry. With a commitment to innovation and excellence, Vessel Vanguard delivers cutting-edge solutions to streamline operations and enhance vessel performance and safety.
Latest Industry Insights
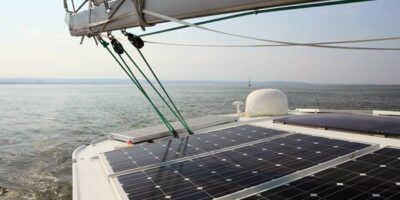
Embracing E-Boating Efficiencies
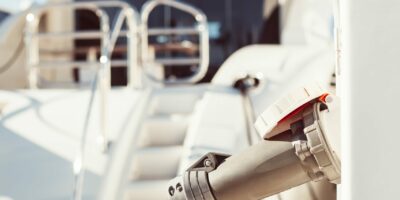
Boat Fuel Systems
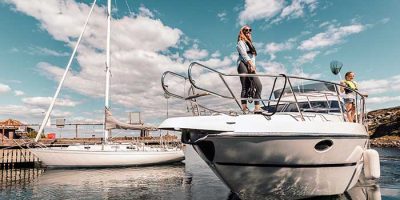
The Future of Boats & Boating
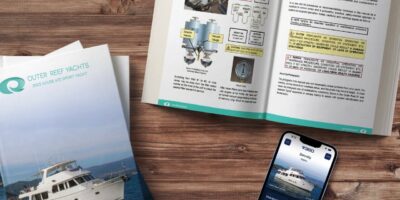
Yacht Navigation Light Inspection
View All of Our Industry Insights
Navigate maritime with the latest news, practical how-to guides, insightful analyses and more.